Mastering Stock in Inventory Management
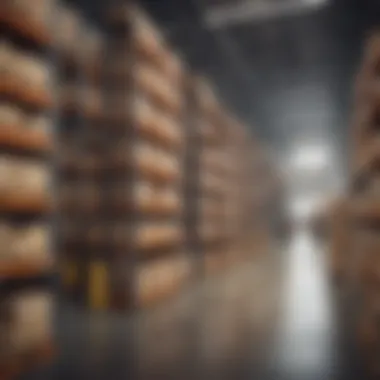
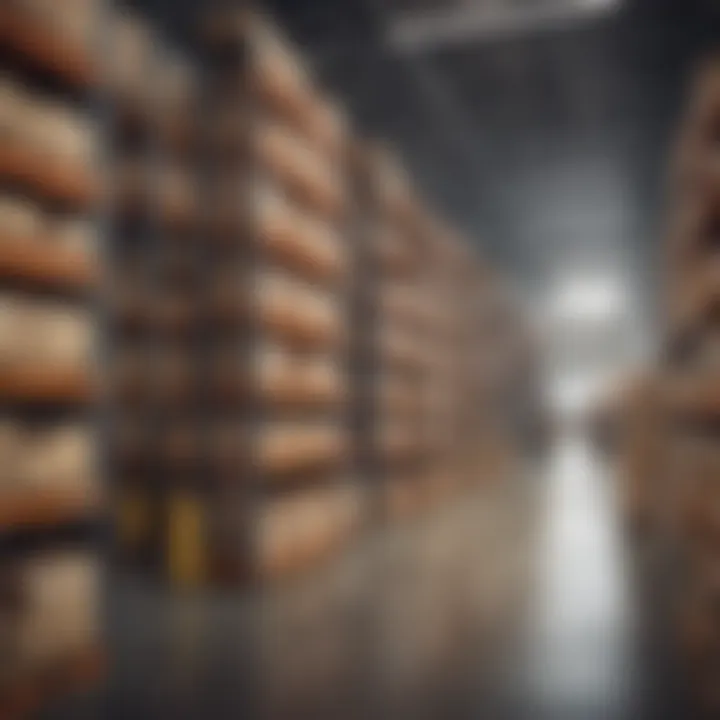
Intro
In the world of business, particularly in retail and manufacturing, stock management is akin to the lifeblood of operations. Think of it as ticking a box on a lengthy to-do listâif something's amiss in your inventory, it could throw a wrench in your whole scheme. From balancing the amount of goods on hand to predicting whatâs going to fly off the shelves next, effective stock management is crucial.
A wise man once said, "You canât manage what you donât measure." In the context of inventory, if you lack an accurate grasp on stock levels, you are walking a tightrope without a safety net. The intricacies of stock tracking and management not only influence day-to-day operations but also impact broader financial health and customer satisfaction.
This article takes a closer look at how businesses can leverage various strategies and technologies to create seamless inventory systems. It aims to equip investors, financial advisors, and analysts with insights into stock dynamics and their relationship with overall business success.
The multifaceted nature of stock management can feel overwhelming at times; however, this comprehensive guide simplifies the process, highlighting key methodologies and technologies that lead to improved outcomes. Readers will explore case studies and best practices, delve into the challenges faced in todayâs fast-paced marketplace, and gain a deeper understanding of how to navigate the complexities of stock management successfully.
Foreword to Inventory Management
In the fast-paced world of business, inventory management is more than just keeping track of products on a shelf. Itâs a multifaceted approach that ensures organizations operate smoothly, financially and logistically. Efficient inventory management helps in reducing costs, optimizing supply chains, and ultimately, improving overall business performance. When done correctly, it can significantly minimize risks related to stockouts or overstocking, which might affect a company's cash flow and customer satisfaction.
But how does this all come together? This article will explore the various elements of inventory management, bringing to light its critical role in an organizationâs success. We'll dig into different types of stock, valuation methods, and the impact that cutting-edge technology has on inventory management practices today.
Definition of Inventory Management
Inventory management refers to the processes and systems that supervise and control the ordering, storage, and use of components that a company uses in the production of the items it sells. This includes raw materials, work-in-progress, and finished goods. While it may sound straightforward, the mix of logistics, finances, and strategic planning behind the scenes is more complex. Itâs about managing what a business has, ensuring itâs not holding too much which could tie up cash flow, nor too little which could hinder their ability to meet customer demand.
Within this framework, companies employ various tools and techniques for tracking inventory levels and movements. Think of it like a game of chessâevery move must be calculated to ensure that the organization stays ahead of its competitors. The goal is to maintain an optimal balance between demand and supply, with the right stock at the right time.
Importance of Inventory Management
Inventory management plays an essential role in the operational strategy of any company, large or small. Below are a few key reasons:
- Cost Control: Keeping a handle on inventory avoids unnecessary costs like storage and obsolescence. This control helps in maintaining healthy profit margins.
- Customer Satisfaction: By ensuring the right products are available when customers need them, businesses can enhance the shopping experience, encouraging repeat sales.
- Cash Flow Management: Efficient stock management directly influences cash flow, as it prevents over-investing in inventory that may not sell.
- Data Insights: By analyzing inventory data, companies can forecast demand more accurately, leading to better planning and maximization of resources.
"An effective inventory management system is the backbone of a successful business strategy."
In essence, the importance of inventory management in todayâs market lies in its ability to create a competitive edge. As companies strive to be more agile and responsive, understanding and optimizing stock levels will be pivotal to navigating the complexities of modern supply chains. Moreover, with advancements in technology, those who adapt quickly stand to benefit immensely. The integration of advanced analytics and inventory management systems allows for more accurate decision-making, improving general performance.
Inviting these practices into an organization's routine is not just strategic. It's also a necessity for survival in a marketplace that evolves at breakneck speeds.
Understanding Stock
Understanding stock is vital for effective inventory management. Stock represents a significant portion of a business's assets and directly influences financial health. When businesses grasp the intricacies of stock, they can minimize waste, enhance cash flow, and ultimately deliver better products to their customers. Each type of stock serves a unique purpose in the supply chain, demanding an understanding of its specific characteristics and management techniques.
Types of Stock
In inventory management, categorizing stock into distinct types helps in streamlining processes and reducing errors. There are three main types of stockâraw materials, work-in-progress, and finished goods. Each category has its own unique attributes and plays a pivotal role in the overall production cycle.
Raw Materials
Raw materials are the foundational elements used to create products. They can include anything from steel and plastic to cotton and chemicals. The significance of raw materials lies in their ability to influence production costs and the quality of the final product.
One key characteristic of raw materials is that they often require careful sourcing and quality checks. The better the quality of raw materials, the higher the potential for producing superior finished goods. However, dealing with raw materials can also present challenges. Prices for commodities can fluctuate, affecting profitability. Additionally, businesses must maintain appropriate levels of stock to avoid production delays.
Work-in-Progress
Work-in-progress (WIP) refers to products that are in the midst of being manufactured. This type of stock is crucial in gauging operational efficiency. It represents the costs incurred but not yet realized in finished goods.
A key feature of WIP is that it can help identify bottlenecks in the production process. By analyzing WIP levels, companies can streamline operations and improve throughput. Yet, holding too much WIP can tie up capital and space, leading to inefficiencies. Striking a balance in WIP is essential for optimizing production flow.
Finished Goods
Finished goods represent the end products ready for sale. They are crucial for meeting customer demand and maintaining satisfaction. The key characteristic of finished goods is their direct relation to sales revenue. Without adequate finished goods, businesses risk losing sales opportunities.
Finished goods must be managed carefully. Too much finished stock can lead to excess inventory costs, while too little can cause stockouts. Proper forecasting and inventory management strategies can assist in maintaining the right levels of finished goods, ensuring that businesses stay responsive to market needs.
Stock Valuation Methods
Accurate valuation of stock is a fundamental aspect of inventory management that impacts financial statements, tax obligations, and budgetary decisions. There are three prevalent stock valuation methods: FIFO, LIFO, and Weighted Average. Each method has implications for cash flow and profitability assessment.
FIFO (First In, First Out)
FIFO assumes that the first items purchased are the first to be sold. This method is particularly beneficial during times of price increases, as it allows businesses to minimize tax liabilities on profit. The unique feature of FIFO is its alignment with actual sales processes; businesses typically sell older inventory before newer stock.
However, the downside to FIFO can be found in inflationary environments. Companies might show inflated profits due to selling cheaper older stock while retaining higher-priced items, leading to potential cash flow issues.
LIFO (Last In, First Out)
LIFO operates under the premise that the most recently acquired inventory is sold first. This method can provide tax benefits during inflation, similar to FIFO. A notable characteristic of LIFO is that it can help businesses match current costs with revenues, thereby reducing taxable income.
However, LIFO is often viewed unfavorably. It can distort profit reporting and inventory value on the balance sheet, leading to less clarity for investors assessing the business's actual performance over time.
Weighted Average
The Weighted Average method calculates the average cost of all inventory items, regardless of the order of acquisition. This method smooths out price fluctuations over time, providing a balanced view of stock valuation. One appealing aspect of using the Weighted Average method is its simplicity; it eases the complexities of tracking individual inventory costs. However, the risk is that it may not reflect the actual profitability of specific items, especially in volatile markets.

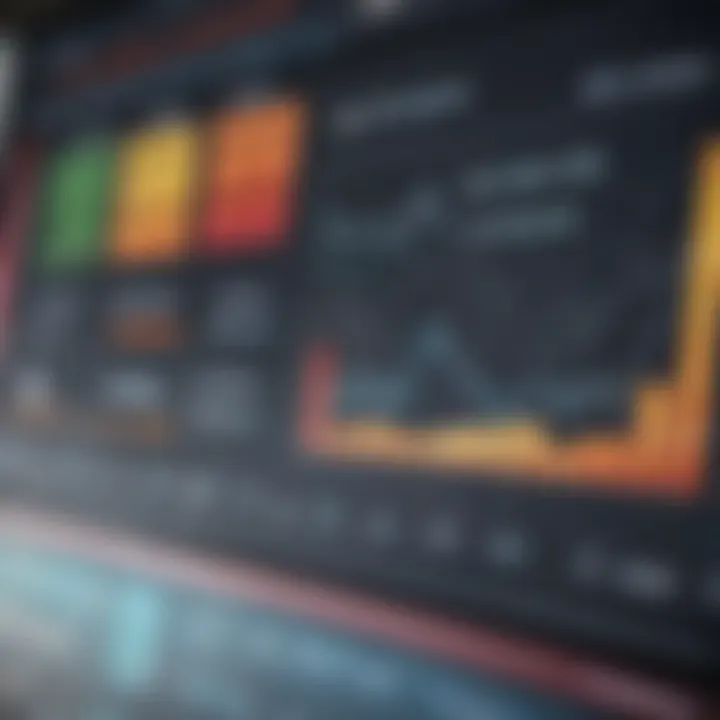
Understanding the nuances of stock types and valuation methods can profoundly impact a business's operational strategy and financial health. Knowing when to apply each valuation method can also help navigate market challenges effectively.
In summary, fully grasping the components of stock and how they are valued is paramount for any investor or business leader looking to optimize inventory management and improve their bottom line.
The Role of Technology in Inventory Management
In today's fast-paced business landscape, the role of technology in inventory management cannot be overstated. Companies striving for efficiency and competitiveness are increasingly relying on state-of-the-art technology solutions to manage their stock. Automation, cloud computing, and advanced data analytics are just a few of the tools that organizations are adopting. The shift towards implementing these technologies leads to better stock tracking, minimizing losses, and ultimately enhancing profitability.
Technology's importance lies in its ability to streamline processes that once took countless hours. By adopting digital solutions, businesses can achieve accuracy in inventory counts, which is critical for operations.
"In the world of inventory, precision is a virtue. One misstep can lead to cascading effects."
Inventory Management Software
Features to Look For
When evaluating inventory management software, it's essential to focus on features that align with your business's specific needs. A top characteristic to seek is real-time tracking. This allows for instant updates on stock levels, making it easier to manage orders and avoid stockouts.
For instance, having a mobile app integrated with the software is highly advantageous. It boosts accessibility and ensures team members can check stock levels, regardless of their location. A unique aspect of robust software is its user-friendly interface, which is an attraction for many organizations. If the system is complicated to use, staff may resist adopting it, negating the benefits.
Top Market Solutions
Among the leading market solutions, TradeGecko has made a name for itself. Its strength lies in seamless integration with e-commerce platforms. This enables it to automatically sync stock levels across multiple selling channels, promoting efficiency and reducing manual work. However, it might not cater to all business sizes effectively.
NetSuite, known for its comprehensive features, offers a robust solution for larger enterprises. The challenge with NetSuite can be its complexity and steep learning curve for new users. It's vital for businesses to weigh these advantages against potential hurdles when selecting a software solution.
Automation in Inventory Systems
Advantages of Automation
Automation brings a multitude of advantages to inventory management. Chief among these is its ability to minimize human error, which is a common pitfall in manual entries. With automated systems, businesses can experience improved accuracy in stock levels. Another key characteristic is the efficiency it fosters; manual tasks that once consumed valuable time can now be handled with the click of a button.
A noteworthy feature of automation is forecasting capabilities. By analyzing past sales data, systems can predict future demand, ensuring stock levels are adjusted proactively. This leads to a smoother operational flow and better customer satisfaction, as items are less likely to be out-of-stock when needed.
Integration with Other Systems
Integration with other systems is crucial for creating a streamlined inventory process. When inventory management software can connect with an organizationâs accounting software, it ensures that financial data flows seamlessly, reducing discrepancies.
A prime example is the integration of inventory systems with ERP (Enterprise Resource Planning) solutions. This dual functionality enables organizations to manage all aspects of their business from a centralized platform. However, careful consideration needs to be given to the complexities that may arise during integration processes; outdated legacy systems can slow down implementation and hinder performance.
In wrapping up this section, the integration of technology in inventory management heralds a transformative era. With the right tools and practices in place, businesses can rise above traditional challenges, pushing towards an era marked by precision and efficiency in their inventory strategies.
Inventory Management Strategies
Effective inventory management strategies are crucial for businesses striving to optimize their stock levels and streamline operations. These methods not only help in maintaining the right amount of stock but also play a significant role in cost reduction and improved customer satisfaction. A well-executed strategy ensures that investors and business owners alike can navigate the unpredictable waters of supply and demand.
Just-In-Time (JIT) Inventory System
Just-In-Time is an efficient inventory strategy where material is ordered and received only as it is needed in the production process. The fundamental goal is to decrease waste and improve cash flow by reducing the amount of capital tied up in stock. Itâs a forward-thinking approach thatâs quite popular for its efficiency.
Principles of JIT
The principles of JIT revolve around minimizing inventory levels while ensuring that production criteria are still met. One key characteristic is the pull-based approach, where production is triggered by actual demand rather than forecasts. Because of this pattern, JIT helps reduce holding costs and enhances factory space utilization.
One unique feature of JIT is its reliance on strong supplier relationships. When suppliers understand the rhythms of a companyâs production needs, they can deliver materials just when theyâre needed. This responsiveness provides an enormous advantage in a fast-paced market, but it also carries risks, such as potential disruptions in supply chains.
Advantages and Disadvantages
One remarkable advantage of the JIT system is inventory efficiency. Reducing stock on hand means lower expenses related to storage and spoilage, maximizing profits instead. It also fosters better supplier relationships, as businesses become more reliant on timely deliveries.
However, the JIT approach isnât without its downsides. The main risk lies in dependency on suppliers. Any hiccup in the supply chain can lead to unexpected production halts, impacting a companyâs ability to meet customer demands. Companies must weigh these factors before committing to a JIT strategy.
ABC Analysis
ABC analysis is another popular method that categorizes inventory into three classes: A, B, and C. It essentially prioritizes items based on their significance in the overall inventory. A items are most valuable, while C items contribute the least to overall revenue. This classification helps businesses allocate resources efficiently.
Categories of Stock
The three categories in ABC analysis drive effective inventory management. 'A' items typically constitute a small portion of total inventory but account for a significant portion of total value. Conversely, 'C' items encompass a large number of items but have a lower relative value. Each category offers different management techniques, making it easier for companies to address their unique needs.
The careful categorization allows businesses to focus their efforts and management resources where they matter most, leading to an overall increase in efficiency.
Implementation of ABC Analysis
When implementing ABC analysis, businesses begin by categorizing their inventory based on criteria like sales volume and profitability. The process entails systematically reviewing data to determine which products fall into which category. This detailed approach enhances decision-making and shifts focus toward higher-value itemsâultimately benefiting the bottom line.
By concentrating management efforts on A items while streamlining the handling of B and C items, companies can significantly improve their inventory turnover rates and enhance overall profitability.
Economic Order Quantity (EOQ)
Economic Order Quantity is a formula that determines the optimal quantity of inventory to order, balancing ordering costs and holding costs. The essence of EOQ is to find that sweet spot where these costs meet, preventing overstocking and stockouts.
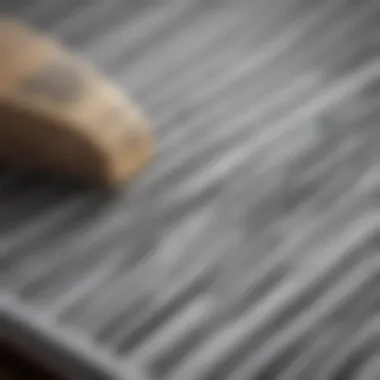
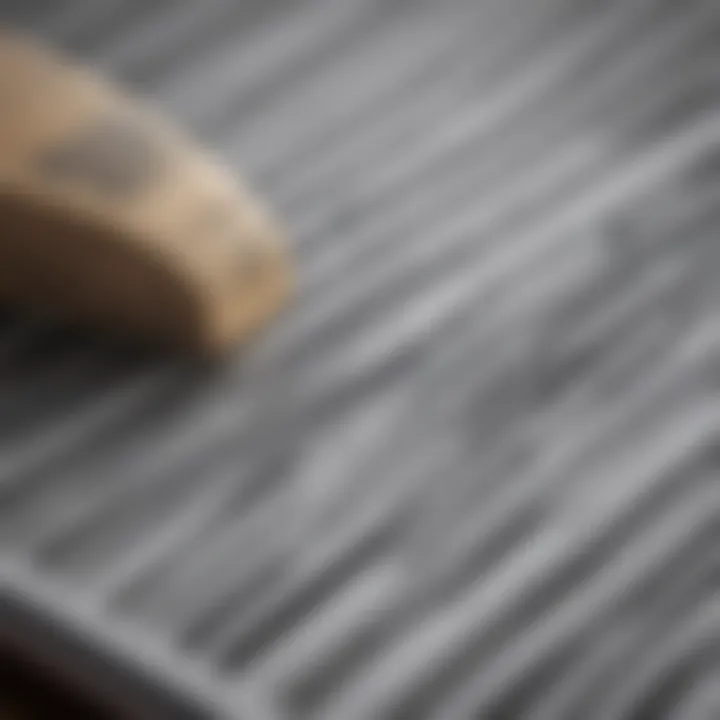
Definition and Formula
The EOQ formula is defined as follows:
Where D is the demand rate, S is the ordering cost, and H is the holding cost per unit. This formula assists businesses in making data-driven decisions regarding inventory levels and purchasing.
The beauty of EOQ lies in its simplicity, making it an approachable strategy for companies of all sizes. It emphasizes the importance of calculating expected demand accurately to reach optimal efficiency.
Benefits of EOQ
One notable benefit of using EOQ is the cost savings derived from reduced ordering and holding expenses. businesses can avoid stockouts and the frantic rush of ordering more supplies than necessary. This steady approach allows companies to maintain stability and predictability in inventory management.
Implementing EOQ might also foster better relationships with suppliers, as predictable ordering schedules can streamline the supply chain.
However, itâs essential to remember that the effectiveness of EOQ can diminish in environments with highly variable demand or fluctuating ordering costs. Therefore, while EOQ is a valuable tool, companies need to regularly revisit their calculations to remain agile and responsive to market changes.
Challenges in Inventory Management
In the landscape of business operations, inventory management stands as a critical cog in the machine. Getting the stock levels right isn't just about filling shelves and making products available; itâs about understanding the ever-evolving challenges that can throw a wrench in otherwise smooth processes. Challenges in inventory management can have detrimental effects on cash flow and customer satisfaction, making it imperative for businesses to navigate these waters skillfully. Here, we delve into specific challenges like overstocking, stockouts, seasonal fluctuations, and forecasting difficulties, shedding light on their impact and how to address them effectively.
Overstocking and Stockouts
Overstocking and stockouts are two sides of the same coin, both stemming from the need to meet demand without tying up too much capital in inventory.
Causes of Overstocking
Overstocking can happen when companies misjudge consumer behavior or fail to keep tabs on stock movement's intricacies. The primary culprit here is often an inaccurate demand forecast, coupled with a lack of integrated inventory systems to get real-time data. For example, a company might overestimate the popularity of a seasonal item, leading to unsold goods accumulating. One key characteristic of overstocking is the financial strain it creates, locking up cash that could be utilized more effectively elsewhere. This issue can be particularly potent in industries where products have a limited shelf-life, such as food or fashion items. The unique feature of overstocking lies in its direct correlation to increased holding costs, including storage fees and insurance, which can erode profits significantly.
Consequences of Stockouts
On the flip side, stockouts can be just as damaging. When a business runs out of stock, it faces immediate customer dissatisfaction and potential loss of repeat business. Businesses may experience hiccups; an unstocked item can lead customers to seek alternatives, harming a brandâs reputation. Additionally, while stockouts might save a company from paying for storage, the loss of sales opportunities can outweigh these supposed savings. Thus, a critical characteristic of stockouts is the lost revenue and increased customer churn. Moreover, the unique feature of stockouts is that they can lead to rushed orders or overreliance on expedited shipping, which, while solving an immediate issue, can compound costs and lead to further inefficiencies.
Seasonal Fluctuations
Businesses often grapple with the ebb and flow of seasonal demands, necessitating strategic adjustments to inventory.
Adjusting Inventory for Seasonality
Adjusting inventory for seasonality is key to thriving in environments where demand swings widely. For instance, retailers often bulk up on summer merchandise before the season hits, only to deplete stocks rapidly or find themselves with unsold items post-summer. The pivotal aspect of this process is the ability to anticipate changes in consumer demand based on season, knowing that flooring fluctuations can have lasting effects on cash flow. Many businesses thrive when they embrace this aspect, allowing them to minimize waste and maximize revenue. On the other hand, not adjusting adequately can lead to missed opportunities and loss of market share.
Impact on Supply Chain
The impact on the supply chain is a consequential thread interwoven with seasonal adjustments. When a business fails to align its supply chain with seasonal changes, it may find itself in a precarious position, unable to meet demand. A major characteristic here is the ripple effectâdisruptions in stock can lead to delays in fulfillment, causing a chain reaction of discontent among customers and retailers alike. Notably, the unique feature of this challenge manifests in the way it affects long-term relationships with suppliers and distribution partners, who may be hesitant to align with businesses that struggle to forecast accurately.
Demand Forecasting Difficulties
As businesses endeavor to predict future sales and manage inventory, demand forecasting emerges as a vital skill.
Importance of Accurate Forecasting
The importance of accurate forecasting cannot be overstated. Precise forecasts allow a business to keep the appropriate amount of inventory on hand, thereby optimizing cash flow and reducing waste. A good forecast is like a compass guiding business decisions, aligning quantities with expected demand at various points. The reliable characteristic of accurate forecasting is its power to shape inventory strategy effectively and contribute to profitability. However, the challenge lies in collecting the necessary data for reliable forecasts; poor accuracy can expose a business to both overstock and stockouts.
Methods for Enhancing Accuracy
Enhancing forecasting accuracy involves utilizing statistical analysis and machine learning insights, which are often underutilized by smaller organizations. Staying ahead of competition requires companies to adopt these methods while analyzing market trends and past sales data to retrain their forecasts accordingly. This aspectâs uniqueness is rooted in its dual benefit: improving immediate inventory decisions while cultivating long-term strategic insights. While these methods can boost accuracy, the disadvantage is the initial investment of time and resources, which may deter some businesses from pursuing this invaluable enhancement.
In summary, challenges in inventory management are multifaceted but manageable. Recognizing these difficulties allows businesses to devise strategies that minimize risks and enhance operations.
Understanding these challenges can help investors and financial advisors make informed decisions when assessing a business's inventory strategy and overall operational efficiency.
Best Practices for Effective Inventory Management
Managing stock effectively is a cornerstone of successful inventory management. When an organization adopts best practices, it not only streamlines operations but also maximizes profits and enhances customer satisfaction. These practices can range from physical audits to utilizing advanced analytics, helping firms make informed decisions and reduce costly errors.
One of the key benefits of instilling these practices is improved accuracy. Without regular checks and adjustments, stock discrepancies can become a massive headache, leading to missed sales opportunities or excess warehousing costs. In addition, these practices help in creating a more transparent inventory flow, making it easier for stakeholders to understand stock levels and turnover rates.
Regular Audits and Inventory Counts
Regular audits form the backbone of an effective stock management system. They ensure that the recorded inventory aligns with what is physically available, reducing potential financial losses.
Cycle Counts
Cycle counts are a method where a portion of inventory is counted on a rotating schedule throughout the year. This practice is beneficial due to its efficiency. It avoids the disruption caused by full inventory counts while providing ongoing insights into stock accuracy.
A key characteristic of cycle counts is their flexibility. Companies can choose different items to count based on their valuation or turnover, allowing for targeted management of high-demand or costly items. This method can be particularly advantageous because it enables businesses to identify discrepancies in real time, addressing issues before they escalate.
However, one challenge with cycle counts is ensuring that staff remains diligent in recording inventory accurately. It's easy for the process to be overlooked in busy periods, which may diminish its effectiveness.
Full Inventory Audits
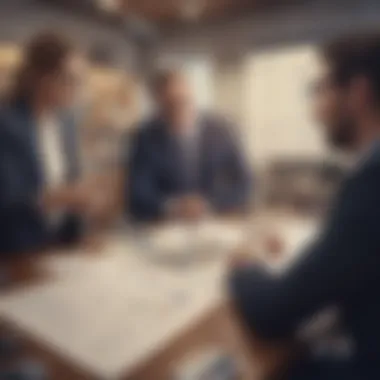
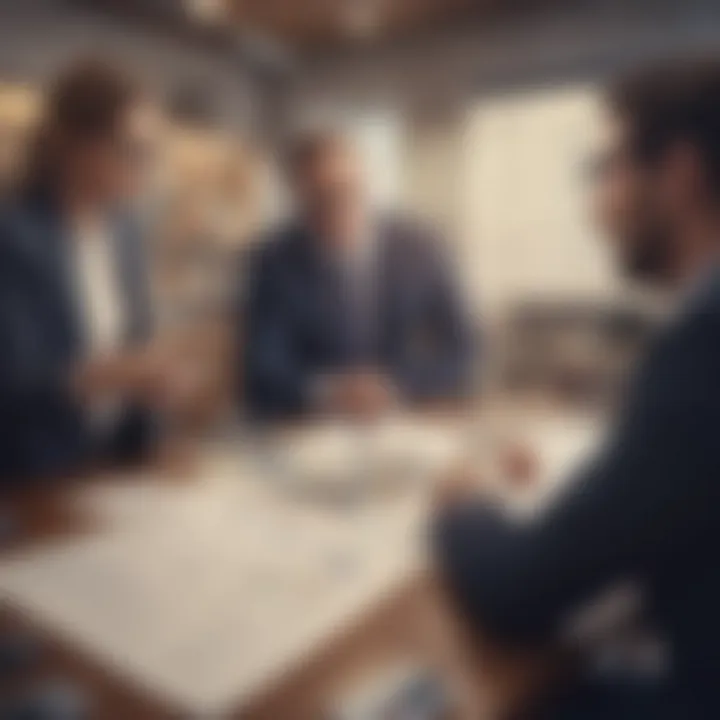
Full inventory audits involve checking all stock at once, usually on an annual basis. This practice ensures thoroughness, providing a complete snapshot of stock accuracy at a set point in time.
The standout feature of a full audit is its comprehensiveness, allowing businesses to identify not just discrepancies but also gaps in processes. It can also renew employee focus on inventory management, as it typically requires more attention across the organization.
While full audits provide essential data, they come with drawbacks. Conducting a complete stock count often takes considerable time and can disrupt regular operations. When handled poorly, it may lead to inaccuracies if the warehouse layout hasn't been well managed.
Data Analytics and Reporting
Data-driven decision making has become a requisite for successful inventory management. Leveraging analytics can significantly impact how inventory is maintained and optimized.
Using Data for Decision Making
The utilization of data analytics in making decisions has emerged as a powerful tool for improving inventory operations. By analyzing sales trends and stock levels, businesses can fine-tune inventory to meet demand more effectively.
A notable benefit of deploying analytics is predictive forecasting. Companies can anticipate trends and adjust their orders accordingly, reducing instances of overstocking or stockouts. Additionally, data analytics assists in identifying which products are flying off the shelves and which are collecting dust.
The unique feature of using data for decision making lies in its ability to inform real-time actions, enhancing agility in the stock planning process. However, the downside could be a dependence on technologyâif data inputs are off or interpretations flawed, it may lead to poor decisions.
Tools for Inventory Analytics
The selection of the right tools for inventory analytics plays a crucial role in achieving effective management. Solutions like SAP and Oracle are widely respected, offering comprehensive functionalities for tracking and predicting stock behaviors.
Using specialized tools is advantageous because they often come equipped with alert systems, helping users stay on top of inventory changes. Their analytical capabilities allow businesses to visualize trends and streamline operations accordingly.
However, these tools can come with a hefty price tag, particularly for small businesses. Complex systems might also require in-depth training to ensure teams can fully utilize their potential, which could be a stressor for operations already juggling multiple priorities.
"Data is not just a set of numbers; it tells a story that needs interpretation to influence an organization's trajectory."
By implementing these best practices in inventory management, organizations can cultivate a resilient stock system that not only serves current operations but also positions them favorably for future growth.
The Future of Inventory Management
As businesses navigate the ever-changing landscape of global markets, the future of inventory management becomes increasingly important. Companies today are not just looking to track their stock; they want to employ strategies that enhance efficiency, reduce costs, and, ultimately, boost profits. Awareness of the trends and technologies influencing inventory management can enable organizations to keep pace with competitors and meet consumer demands effectively.
Emerging Technologies
Artificial Intelligence
Artificial Intelligence (AI) is reshaping inventory management by introducing automation and predictive analytics. One of the standout aspects of AI is its ability to analyze large volumes of data quickly. This capability allows businesses to forecast demand with a higher degree of accuracy, reducing the risks of overstocking or stockouts. AI can take into account various factors, such as seasonal trends, buying behaviors, and even market fluctuations.
The unique feature of AI in inventory management is its learning capability; as it processes more data, it becomes better at making predictions.
However, despite its benefits, there are disadvantages to consider. Implementation costs can be high, and managing such systems requires skilled personnel. This can be a barrier for smaller businesses, potentially limiting their adoption of AI technologies.
Blockchain Technology
Blockchain technology emerged as a game-changer in how inventory systems can be securely managed. Prominent for features like transparency and traceability, it enables businesses to track the journey of stock from suppliers to customers seamlessly. In the context of inventory, blockchain ensures that records are tamper-proof, significantly increasing the trustworthiness of information.
A unique aspect of blockchain is its decentralized nature, which reduces the chance of data manipulation. This builds confidence among all parties involved in the supply chain. While the benefits are clear, companies must be mindful of the complexities associated with implementing blockchain solutions, like high energy consumption and the substantial technical know-how required for effective management.
Sustainability in Inventory Practices
Importance of Sustainability
Sustainable practices in inventory management are forefront in todayâs business strategies. The growing public awareness about environmental issues has made it vital for companies to adopt practices that reduce waste and enhance efficiency.
A significant characteristic of sustainability is its long-term vision. It not only aims for immediate operational advantages but also considers the broader impact on the environment and community. When done right, sustainable inventory practices can lead to cost savings by reducing waste and energy consumption.
However, the journey toward sustainability can present hurdles, including initial investment costs and the need for process changes. Companies often struggle to strike a balance between profit margins and sustainable practices.
Strategies for Green Inventory Management
Strategies for green inventory management focus on reducing environmental footprints while keeping operational efficiency. Techniques can include even ordering practices, efficient transportation schedules, and recycling old stock effectively.
The key characteristic of these strategies is their adaptability. They can be tailored to fit various industries and inventory types, making them a popular choice. One unique feature is the combined approach of employing both technology and eco-friendly practices.
Yet, while these strategies can be beneficial, the implementation may involve compromises on speed and availability. Companies must weigh the benefits against the potential drawbacks while considering their operational goals.
Companies today must realize that transitioning to a more sustainable inventory system is not just an option; itâs a necessity.
Finale
In every corner of business, the ability to manage stock effectively stands as a pillar upon which successful operations are built. This article sheds light on why understanding stock management is not merely a detail but a significant component impacting overall performance. By drawing clear connections between stock levels, operational strategies, and financial outcomes, it invites readers to appreciate the need for vigilance in inventory practices. As businesses adapt to changing market conditions, aligning their stock management techniques to meet economic pressures is essential.
Summary of Key Points
In summary, this article highlighted several crucial aspects:
- Diverse Types of Stock: Recognizing the different categoriesâraw materials, work-in-progress, and finished goodsâhas relevance in optimizing organizational processes.
- Valuation Methods: Techniques like FIFO, LIFO, and weighted average were discussed, emphasizing their implications on financial reporting and taxation.
- Role of Technology: The integration of software and automated systems significantly reduces manual errors, enhances efficiency, and offers real-time data insights.
- Strategic Approaches: Strategies including JIT, ABC analysis, and EOQ provide frameworks for making informed inventory choices that align with market demand.
- Challenges and Solutions: Understanding the pitfalls, including overstock situations or inaccurate forecasting, led us to explore actionable solutions which can buffer organizations from potential losses.
- Future Trends: We also touched on emerging technologies like AI and blockchain, underscoring their potential in revolutionizing inventory practices and fostering sustainability.
This guidance serves as a roadmap for investors and business leaders, indicating the necessity of precise stock control as a differentiator in competitive landscapes.
Implications for Investors
For investors, the health of inventory management systems can signal the operational efficiency of a company, making it a key area for evaluation.
- Investing in Technology: Companies that leverage advanced inventory technologies often showcase stronger performance metrics; hence, their appeal increases.
- Market Responsiveness: A sophisticated inventory approach can indicate a company's ability to respond dynamically to market changes, which is a major consideration for long-term success.
- Risk Management: Understanding inventory challengesâlike overstocking or stockoutsâoffers insight into a firmâs risk management capabilities. This can be a red flag or a green light for potential investments.
- Financial Health: Effective stock management contributes directly to cash flow management, impacting vital financial statements. Investors should look for signs of efficiency or trouble in this area to make informed decisions.